Breaking the Cycle of Repeat Repairs: How AI is Revolutionizing Automotive Quality
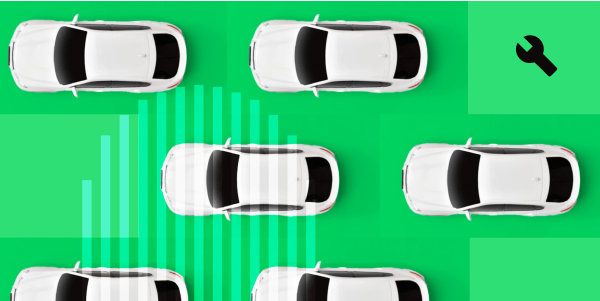
Repeat repairs are a persistent challenge for automotive OEMs. Despite implementing countermeasures, the same issues keep cropping up, leading to mounting costs and customer dissatisfaction. These recurring problems frustrate technicians, burden service centers, and erode brand trust.
For example, warranty claims in the automotive industry alone cost OEMs billions annually, and repeat repairs often account for a disproportionate share of that expense. The impact extends beyond financial losses—frequent trips to the dealership diminish customer confidence, ultimately impacting long-term loyalty.
This post explores how AI-powered analytics can address the root causes of repeat repairs, offering OEMs a transformative approach to quality management.
The root of the problem: why repeat repairs persist
The complexity of modern vehicles often makes identifying and resolving quality issues a daunting task. A single vehicle can contain thousands of interconnected components, each playing a role in the overall system’s performance. When a problem arises, the cause is rarely straightforward. Instead, it may be the result of subtle interactions between hardware, software, and environmental factors—factors that are difficult to isolate and even harder to address comprehensively.
This complexity often leads to short-term fixes that focus on mitigating symptoms rather than addressing the root cause. For example, an OEM may introduce a countermeasure to reduce the likelihood of a recurring issue, only to find that the problem resurfaces under slightly different conditions. These partial solutions not only fail to resolve the issue but also contribute to a cycle of recurring repairs that frustrates technicians and customers alike.
Adding to the challenge is the sheer volume and variety of data involved. OEMs have access to a wealth of information—vehicle telematics, warranty claims, service logs, and feedback from the field—but these datasets are often siloed across different departments or systems. Without a unified view of the data, it becomes nearly impossible to detect patterns or identify causal relationships that could lead to effective, lasting solutions.
Together, these factors create an environment where repeat repairs persist despite significant efforts and investments. The impact of this persistence is felt across financial, operational, and reputational dimensions.
The hidden costs of repeat repairs
The consequences of repeat repairs extend far beyond the warranty claims they generate. Financially, these recurring issues drive up costs through unnecessary replacement parts, additional labor, and even logistical inefficiencies. OEMs not only pay the immediate price of fixing the problem but often see warranty reserves ballooning year after year.
Operationally, repeat repairs place a significant burden on service centers, which must allocate time and resources to address the same issues repeatedly. Technicians face frustration from both customers and their own inefficiencies, diverting attention from other critical service needs.
Perhaps most damaging, however, is the erosion of customer trust. Frequent trips to the dealership for the same problem create dissatisfaction and undermine the perception of quality that OEMs work hard to cultivate. Over time, this can lead to reduced brand loyalty and lower lifetime customer value—a cost that is difficult to quantify but deeply felt in the marketplace.
Breaking this cycle requires a new approach—one that is proactive, data-driven, and capable of addressing the root causes of recurring issues. This is where AI steps in.
How AI transforms the approach to repeat repairs
AI offers OEMs a powerful toolkit for breaking the cycle of repeat repairs, moving from reactive problem-solving to proactive quality management.
- Proactive Detection: AI excels at analyzing telematics and service data to identify subtle patterns and anomalies that may signal an emerging issue. For instance, repeated failures in a specific component under certain environmental conditions can be flagged before they escalate.
- Root Cause Analysis: AI-powered algorithms sift through massive datasets to uncover the underlying drivers of repeat repairs, such as correlations between a supplier’s batch variability and failure rates. This enables OEMs to address the true source of the problem.
- Predictive Insights: Beyond identifying causes, AI can model the potential effectiveness of different countermeasures. OEMs can implement more targeted solutions, reducing the likelihood of recurrence.
This approach transforms quality management, enabling OEMs to get ahead of problems rather than chasing them after they occur.
Real-world application: AI in action
Consider an OEM struggling with a recurring failure in a vehicle’s climate control system. Despite multiple countermeasures, the issue persists, driving up warranty claims and frustrating customers.
Using AI analytics, the OEM integrates data from telematics, service logs, and supplier records. The system identifies a hidden correlation: the failures are concentrated in vehicles operating in high-humidity environments and stem from a specific manufacturing process at a supplier facility.
With this insight, the OEM implements a targeted solution, addressing the supplier issue and providing a climate-specific enhancement. The result? A 60% reduction in repeat repairs within six months.
Viaduct’s AI platform is built to deliver these kinds of actionable insights, using techniques like anomaly detection, causal inference, and predictive maintenance to empower OEMs.
The bottom line
Repeat repairs don’t have to be an inevitable part of automotive quality management. By leveraging AI, OEMs can move beyond short-term fixes and address the root causes of recurring issues.
Break free from the cycle of repeat repairs. Discover how Viaduct’s AI-driven platform can help your organization reduce warranty costs, improve operational efficiency, and rebuild customer trust.
Ready to transform your quality process? Schedule a demo today and see how AI can revolutionize your approach to repeat repairs.