The Top 3 Pitfalls to Avoid When Analyzing Warranty Data
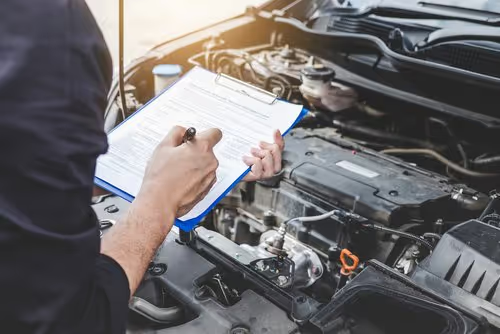
For automotive manufacturers, the importance of product quality can hardly be overstated. According to a recent study by IBM, warranty expenses cost automotive OEMs on average around 2% of revenue, which amounts to over $50 billion annually across the industry. And that is before one factors in the indirect costs of poor quality, such as its negative impact on customer satisfaction, repeat sales, and brand loyalty. As a result, annual quality reports, such as the J.D. Power Initial Quality Study, which ranks brands by the observed defect rates of their products, are closely monitored by manufacturers, media, and most importantly, customers.
Given the costs associated with poor quality, it’s not surprising that OEMs have continuously pursued new ways to improve it. Over the years, the automotive industry has developed tried-and-true processes for quality control and root cause analysis, such as Advanced Product Quality Planning (APQP), Failure Mode and Effects Analysis (FMEA), and Statistical Process Control (SPC), and each new generation of products brings with it further innovations in quality improvement methodology.
In recent years, OEM quality departments have become more and more data-driven, using feedback from the field to drive process and product improvement upstream. Central to this feedback loop is warranty data, which documents the repairs being done to vehicles in the field. Carefully analyzing this data can help automotive OEMs quickly identify, triage, and correct costly quality issues. At Viaduct, however, we have found that warranty data brings with it its own unique set of challenges, which, if not accounted for, can complicate analysis and limit its value. In this post, we’ll discuss the top 3 pitfalls to avoid when analyzing warranty data as well as strategies for overcoming them. First, however, let’s briefly review what warranty data is and where it comes from.
Warranty Data Overview
When a vehicle is sold, the manufacturer usually provides some kind of standard warranty policy, which is in essence an agreement to cover the costs of service for a certain period of time after the vehicle is purchased. As OEM quality has improved, warranty coverage has expanded in duration as well as scope (for light-duty, passenger vehicles, for example, it is now common to see “bumper-to-bumper” coverage, which includes almost all repairs). Service expenses covered by warranty policies are recorded in the form of warranty claims, which record what service was done and how it should be billed. These claims are what we refer to when we talk about warranty data.
The specific fields recorded in each claim can vary depending on the manufacturer, but standard fields we can typically expect to see are:
- VIN: The vehicle identification number
- Date of service: The date when the vehicle was brought in for service.
- Odometer: The odometer of the vehicle at the time of service
- Labor operation (or labor op) code: A code which describes the work that was done on the vehicle
- Dealer notes: A free text field containing any additional information the technician feels is important
These fields are usually manually input by the service technician at the time of the claim and then uploaded to the manufacturer’s systems.
Now that we’ve reviewed what warranty data consists of, we can start to discuss some of the issues with it as well as solutions.
Pitfall #1: Warranty Claims Are Optimized for Billing, Not Analysis
Warranty claims were designed primarily for billing, to record how much the dealer needs to be compensated for the work they did. As a result, the claim format is optimized for describing work done by the technician (via labor ops), rather than the state of the vehicle. In this way, warranty claims for vehicles are similar to health records for people. Both have complex and detailed coding systems recording treatments, with the symptoms or the causes often included as an aside.
This can make it difficult to accurately identify problems and their causes using repair codes alone. A single problem can be treated in multiple different ways in the field, depending on the context. To illustrate how this might happen, imagine a customer comes in with a dead battery due to a faulty alternator. One technician may simply replace the battery without noticing the faulty alternator and send the customer on their way (only to return shortly thereafter reporting another dead battery). Meanwhile, another technician might dig deeper and discover that the alternator isn’t working and replace that instead. Finally, a third technician might dig deeper still, find that the alternator isn’t working because of a broken alternator belt, and just replace that subcomponent. Despite a common root cause, each of these cases would be associated with a different labor op code in the warranty claim.
Because of this, categorizing claims by repair code can obscure the most severe problems in the field. And the more complex an issue is, the more likely it is that repairs will vary from dealer to dealer, which means that the resulting claims are split between multiple repair codes, making it difficult to detect when analyzed in aggregate. As a result, an issue may seem like a low priority when in reality it is one of the top drivers of warranty claims.
In order to avoid this issue, it is preferable to categorize claims by the symptom or customer complaint, which is often recorded in the claim in a free text field. We will see that this approach has its own pitfalls as well, however.
Pitfall #2: Lack of Structure in Free-Text Obscures Valuable Information
When technicians service a vehicle, they do much more than just replace a part. The process usually involves talking to the customer, understanding the problem, running tests, and ideally identifying the root cause. All of this information can be incredibly valuable for quality engineers at OEMs to understand what is happening in their fleet.
Unfortunately, this information typically appears in the warranty claim, if it does at all, in the format of a free text dealer notes. These notes are non-standardized, and each dealership may have its own conventions about how it records the procedures done by the technicians. Sometimes these free text fields may even hold critical information for understanding the final service, such as whether this vehicle is part of a manufacturer campaign or technical service bulletin.
This lack of structure and uniformity makes it difficult for a human to scan and parse through these notes, let alone any traditional, rules-based automated system. Traditionally, the best solution would be to manually inspect a sample of claims and hand-craft key-words. In order to augment this, the Viaduct platform uses advances in machine learning and language modeling to automatically extract domain-specific key-words which a downstream user can query as if it were structured data, facilitating quantitative analysis.
Pitfall #3: Data Lag Slows Down Detection
When it comes to identifying quality issues, time is of the essence. Each day the issue goes undetected, more faulty vehicles are manufactured and delivered to customers, increasing the scope and severity of the issue. The earlier an organization detects an issue, the sooner it can investigate the root cause and implement corrective action.
Unfortunately, since warranty data is often manually uploaded by dealers, it can come at a significant lag (up to a month in some cases). This means that a claim today may only reach the OEM’s systems a month from now, inherently limiting the speed of any early detection system based on warranty data. With thousands of vehicles manufactured every day, an OEM could potentially manufacture tens of thousands of faulty vehicles before they even know that an issue exists, much less understand the root cause.
To overcome this lag, quality organizations can leverage real-time data streams which are transmitted directly from the vehicle, such as usage data and vehicle diagnostic data. For example, in addition to tracking warranty claims, the Viaduct Platform allows for easy monitoring of occurrence rates of their most severe diagnostic trouble codes (DTCs) to detect if they exceed an expected range, indicating a potential systemic issue. By further augmenting this with usage data to see if these DTC occurrences precede vehicle downtime, users can get a clear sense of the health of the fleet in real-time, long before warranty claims come in.
Taking a Smart Approach to Warranty Data
Warranty data is a critical source of quality feedback for automotive manufacturers. However, making full use of warranty data requires extensive exploration, cleaning, and transformation in order to mitigate the impact of issues such as data lag and unstructured free text fields.
Implementing the strategies mentioned in this post is just one of the ways the Viaduct Platform makes it easier for OEMs to quickly and efficiently extract powerful insights from their data. To learn about the other ways that Viaduct helps OEMs leverage their connected vehicle data, including data cleaning, standardization, and enrichment, visit www.viaduct.ai/technology/platform.